Rolling Helix – Motion Converter
High movement speed and simple assembly
What is a Roh'Lix linear actuator?
The name Roh’Lix is inspired by the English term “rolling helix”, which describes how the product works. The rolling distance traveled by the shaft therefore follows a helix, i.e. the rolling helix or Roh’Lix. The functional principle is based on the frictional force between the bearings and the shaft. The present pitch is defined by the linear distance per shaft revolution. Simplified, a Roh’Lix converts a rotary or rotational movement into a linear movement. In standardized Design, the Roh’Lix is provided with a right-hand pitch, which corresponds to the movement of a right-hand thread in a screw, with the difference that the motion is converted on a smooth shaft.
How is a Roh'Lix designed and how does it work?
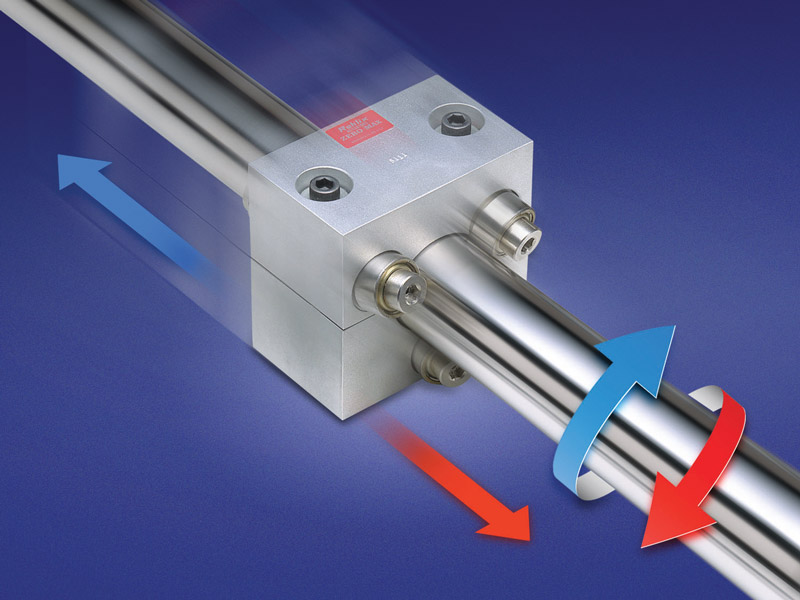
The basic component is a split housing block for easy radial assembly with bearings inserted on both sides. The six bearings, which are preloaded as supplied, define the positioning of the shaft according to the given contact angle. The resulting thrust force of the linear actuator is determined by the spring force between the two halves of the housing. To set the thrust force, the corresponding thrust force value is adjusted using the adjusting screws on the top of the housing. If the intended thrust force setting is exceeded, the Roh’lix slips until the cause of the fault is eliminated. This slippage characteristic enables the use as overload protection and makes the use of additional safety couplings or similar obsolete.
On both sides, the Roh`Lix includes three ball bearings each, which are positioned at a defined angle to the axis of the shaft. The rotational motion causes the shaft to move in a thread-like spiral motion, providing the feed. The linear travel per shaft revolution is defined based on the contact angle of the six ball bearings to the shaft. Specific pitches of up to 3 times the shaft diameter, adapted to the respective application, enable a wide range of applications. Individual linear travel speeds can be achieved by changing the pitch or the drive shaft speed.
What are the advantages of a Roh'Lix?
By transforming rotary motion into linear motion, the Roh’Lix linear actuator offers a variety of innovative and unique product features. The split product design combined with radial mounting and dismounting capability allows for easy and efficient installation or dismounting. Lifetime lubrication provided by the factory enables dry use and ensures smooth operation. The use of ball bearings enables high linear travel and impresses with an efficiency of > 90 %. Operating speeds of up to 1750 mm/second enable fast position changes and can increase machine output.
Integrated overload protection prevents damage caused by exceeding the allowable force. In the case of overload, the linear actuator slips and protects other parts and components from damage and failure. The product characteristics of a maintenance-free Roh’Lix, in combination with the low sensitivity to contamination and debris, offer a significant advantage over classic ball screws. A long service life expectancy coupled with a high degree of service capability enable efficient integration into a wide range of applications. All bearing mounting sets are available as spare parts sets as standard; standard bearings differ in the lubricant used and the degree of filling. A total of five sizes are available with thrust forces ranging from 67 Nm to 889 Nm, with shaft diameters ranging from 8 mm to 50 mm.
- Shaft diameter from ø8 mm to ø50 mm
- Thrust force from 67 Nm to 889 Nm
- Temperature ranges from -23 °C to 82 °C
- Use in horizontal and vertical applications possible, tandem operation possible
- Efficiency at > 90 %
- Maintenance-free operation and easy installation
- Integrated overload protection
- High life expectancy
- Lubricated-for-life bearings
Are customer-specific modifications or special solutions possible?
The constantly increasing demands on applications require customization and the ability to respond to customer requirements. Common modifications or customer-specific solutions are:
- Special Leads from 0.625 mm up to 3 times the shaft diameter
- Lead in left-hand direction
- Special lubrication of the bearings (food approval)
- Stainless bearing designs and other components
- Specific coatings and materials (stainless steel, chromated, anodized, nickel-plated)
- Special bearing/block combinations (oversized bearings for longer service life and higher thrust)
- Customized or modified housings
- Quick-Disconnect feature
- Quick connection and disconnection of the assembly
- Can be used in different pitches on one shaft
- Offers the option of switching to automatic operation
Where do you often find Roh'lix in use?
- Optical measuring devices
- General motion control
- Door systems (opening and closing mechanisms)
- Adjustable path guides
- Special machine construction
- X-Y tables
- Gantry robots
- Packaging machines
- Printing machines
- Pharmaceutical and medical technology processes
- Food technology
- Transfer tables
- Parts feeding systems
- Semiconductor technology
- Materialhandling
What are the recommendations concerning the use of a Roh'Lix?
- For an application with increased positioning accuracy, a linear encoder should be planned for position sensing in order to take into account the accumulated error of 0.05 mm per shaft revolution.
- Sideloads and twisting loads should be avoided and appropriate support should be provided.
- To determine the correct model or the ideal series, we recommend calculating the thrust force, pitch, speed (rotational, linear) and other specifications. (data sheet)
Further information on preferred bearing models and critical speed ranges can also be found in the data sheets. - A case-hardened and ground tempered steel C60 (C-1060) with a minimum hardness of 58 HRC is recommended as the shaft material.
- The use of bellows covers should be considered if a possible negative influence of water, grease or oil mist is to be expected.
- A shaft wiper should be planned for applications with a high degree of contamination.
- In applications with a vertical load, reverse running conditions may occur; this should be considered. (Use of brakes or similar)
- The Roh’lix linear actuator is designed for maintenance-free use, but it is recommended to check for indications of wear at regular intervals.
How to achieve a maximum service life?
The minimum service life of a Zero-Max Roh’lix is 50,000 meters of linear travel based on internal test runs. In practice, 2,500,000 meters of linear travel have been successfully tested. The following key points must be observed to increase the service life and service life:
Thrust force
Correct adjustment of the thrust adjustment screws extends the service life and ensures smooth operation. A further maximization of the service life can be achieved by reducing the application load in relation to the thrust force. It is advisable to select an oversized Roh’lix to achieve the longest possible service life.
Pitch/shaft speed
Larger pitches increase the service life of the Roh’lix, the decisive factor being that the number of bearing revolutions required to cover the same linear distance is reduced. A reduced drive shaft speed also increases the service life.
Overload situations
Occasional overload situations that occur for short periods of time are acceptable and are provided for in the functional principle of the Roh’lix linear actuator. Frequent or long-term overload and slippage situations reduce the service life.
Side loads and Twisting loads
The linear actuator is designed for axial load conditions, sideloads and twisting loads should be avoided. The proportion of the twisting and side loads should never exceed 50% of the linear thrust force to prevent faults or failures. To meet the corresponding application requirements, it may be necessary to use over-dimensioned sizes.
What advantages does the Zero-Max Roh'lix offer compared to classic ball screws?
- The Roh’lix can impress with a number of unique features compared to ball screws.
- Integrated overload protection offers protection in the case of overload (no need for an additional safety coupling or similar)
- Ideally suitable for use on smooth shafts
- Very low backlash (< 0.025 mm)
- No “stick-slip effect” 1
- Low susceptibility to contamination and dirt
- Maintenance-free operation
- High service life expectancy
- Lifetime lubrication (no additional lubrication required)
- Easy to service (simple assembly, disassembly and component replacement)
- High-speed operating speeds possible (1750 mm/sec.)
- Versatile adjustments possible (pitch, counterclockwise rotation, material, etc.)
Which applications are ideal?
- Applications with fluctuating pressure ratios (pneumaticö)
- High demands on linear speeds
- Subject to strict hygiene and cleaning requirements
- Applications that cannot tolerate a “stick-slip effect”
- Applications that require a high degree of customization
1What is the stick-slip effect?
The stick-slip effect is the undesired, often unstable sliding back of solid bodies that are moving against each other. This condition occurs when a body is moved whose static friction is significantly higher than the sliding friction.
Contact us now for your personal consultation.