Composite Disc Couplings
Flexible and high torsional stiffness
What exactly is a composite disc coupling?
The Zero-Max composite disc coupling is an absolutely unique and innovative shaft coupling. The heart of the backlash-free compensating coupling is the specially developed disc design made from a high-performance fiber composite material. The patented Zero-Max “open arm” design of the disk packs in harmony with the basic properties of the fiber composite material enable extraordinary product advantages.
The unique disk design ensures high torsional rigidity and at the same time enables a high and universal shaft misalignment compensation. High chemical resistance combined with a wide temperature range from -57 °C to 121 °C and electrically insulating properties make it the ideal choice for applications subject to external influences.
Composite disc couplings are available in single-cardanic (Single Flex 6A) and double-cardanic (6P) versions. One disk pack is integrated for the single-cardanic version, while two disk packs are installed for the double-cardanic version. To cover large distances between the input and output sides, the torsionally rigid intermediate shaft coupling Floating Shaft (6F) offers backlash-free torque transmission. After several years of field testing, the original product version was ready for the market in 1992. Since 1992, the coupling and disk design has been continuously developed and improved to meet the constantly growing market requirements.
What are the general advantages of composite disc couplings?
In general, the Zero-Max Composite Disc coupling offers a wide range of product advantages and benefits.
- Very low restoring forces
- High torsional rigidity for demanding positioning tasks
- Ideally suited for indexing and reversing applications
- Compact component design
- Stainless steel versions available (nickel-plated, QPQ, etc.)
- Disc pack design for infinite fatigue life
- Wide temperature range (-56 °C to 121 °C)
- High chemical resistance
- Electrical insulation properties
- High impact resistance
- Low outgassing rate
- Resistant to corrosion and friction
- No wear
- High level of customization
- Standardized disc pack
- Nominal torque range from 20 to 5333 Nm
- Bore diameters from 6 to 152 mm
- Seven hub variants available
- Maintenance-free operation with simple installation and replacement
- Very high misalignment capacity
(depending on size: angle up to 3° – parallel up to 3.5 mm – axial up to 12.7 mm) - RoHS-compliant
- Special designs or customer-specific designs possible
Many of our customers appreciate the option of simply replacing the disk pack rather than having to replace the entire coupling. With reference to the different coupling designs in single- and double-cardanic versions, a differentiated view must be considered; both designs can provide significant benefits with specific product characteristics.
Where is a Single Flex coupling (6A) the better option compared to a Double Flex coupling (6P)?
For applications with limited space or servo motor applications, the single-flex design can be an optimal solution. The extremely compact design of the single-cardanic Single-Flex version offers an ideal solution with higher torsional stiffness and lower mass inertia compared to the Double-Flex version.
Single-Flex couplings offer the possibility of compensating large axial and angular misalignments; moderate parallel misalignments can still be compensated. Both designs offer the capability of compensating high angular misalignments (up to 3°), which corresponds to approximately 2-3 times that of standard metal bellows couplings. The single-cardanic Single-Flex offers the possibility of handling slight radial forces.
The double-cardanic Double-Flex coupling includes two disk packs, which make it capable of compensating for enormous parallel misalignment. Comparable to classic bellows couplings, a Double-Flex coupling offers up to 3-4 times the parallel misalignment, which can be a significant advantage in highly demanding applications. Another product advantage of the Double-Flex coupling is the open-arm design, which is used in both disk packs. This open, innovative disc pack arm design reduces the reaction loads that could be applied to connected parts and components.
Another factor in selecting the ideal coupling design is the distance between the shaft ends (DBSE). Intermediate shaft couplings also known as line shaft couplings (Floating Shaft 6F) can be selected for this application.
In which industries or applications can composite disc couplings be especially effective?
In general, the product characteristics of the composite disc coupling meet all the criteria for use in almost any application or critical area of use. Over the last 30 years, critical applications from agriculture and forestry, classic mechanical engineering through to high-performance applications in packaging technology or aerospace have been successfully designed and solved. The requirements and challenges of the various industries and applications could not be more different. For example, applications in the packaging machinery sector benefit in particularly from high torsional stiffness, low reaction loads and the ability to compensate for high shaft misalignments.
Areas of use and applications:
- Packaging machines
- Semiconductor technology
- Machine tooling
- Renewable energies (wind power, tides)
- Test benches
- Measuring machines
- Food technology
- Medicine and pharmacy
- Special machine building
- Printing and converting machines
- General automation
- Machine tools
- Aerospace
When is the use of an A1C hub to be preferred rather than an AC hub?
Both the A1C clamping hub version and the AC clamping ring version are made of aluminum and can be provided with a key.
Due to the higher clamping force, the A1C clamping hub design offers the possibility of transmitting the specified peak torque without a keyway connection. Compared to the AC version with clamping ring, the A1C clamping hub offers a larger bore diameter range and is normally faster to deliver.
The AC clamping ring version is identical in design to the identical steel version (“C”), but has the advantage of lower inertia and the corresponding weight advantage. The “shouldered” hub offers a smaller width of possible bore diameters. This geometric and technical product design may make it necessary to provide a keyway connection in order to handle the peak torque of the coupling.
Is maintenance required for a CD coupling?
No maintenance intervals are planned for all standard composite disc couplings. However, it may be necessary to replace the disk pack if the system is damaged or malfunctions.
After a few hours of operation, it is recommended to tighten the screws of the disk packs in according to the operating instructions. The corresponding tightening torques for the screws can be found in the specific installation instructions.
Regular visual inspection of the coupling is one of the preventive maintenance methods. Check for general anomalies and irregularities such as loose bolts or defective disk packs.
Can the disk pack be replaced on site?
Disc packs of the composite disc coupling can be replaced on site in a user-friendly way. In most cases, the disk packs can be removed directly without having to move the hubs axially. All disk packs are designed in such a way that the concentricity is retained after replacement.
Detailed instructions for replacing and installing the disk packs can be found in the download area.
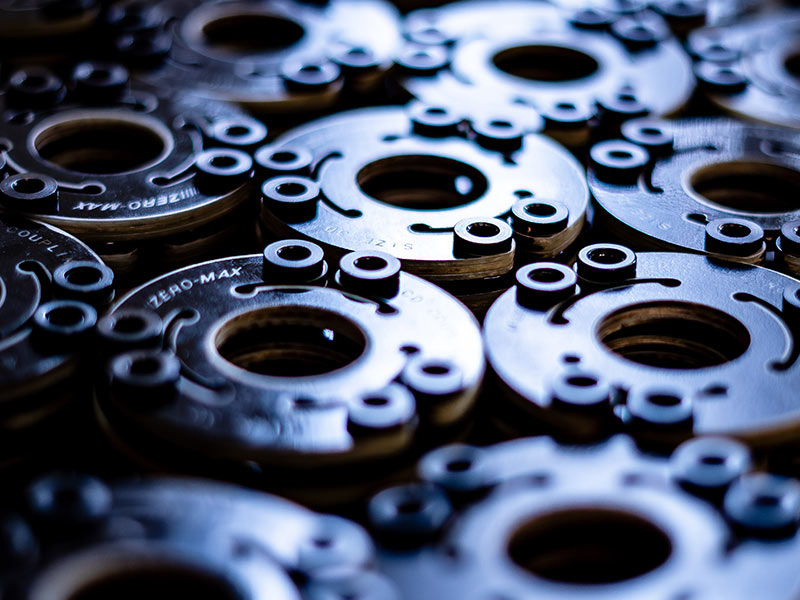
What properties can a special version of a composite disc coupling fulfill?
Over the years, Zero-Max has built up a reputation and expertise as an innovative and customer-oriented specialist in the field of drive technology. Individual and customer-specific application solutions are designed and developed from a requirement quantity of one piece up to large series. We are happy to offer our customers the opportunity to evaluate the corresponding requirement or application on the basis of the specifications available and to offer a corresponding product implementation.
Frequently asked and implemented requirements:
- Higher torsional stiffness requirement
- Greater disk flexibility (increased misalignment compensation)
- Increase in torque performance
- Specific material designs and coatings
- Individual bore designs
- Customized hub designs
- Customized mounting features
- Designs for high-speed operation
- Phase adaptations
- Adaptations to “actual condition”
- Customized designs for limited space requirements
- Longer intermediate shaft designs (>4,500 mm)
- Many other adaptations and modifications
When is a composite disc coupling suitable? When is a Servoflex coupling the better choice?
There is no general answer to this question; the dimensions in particular often play a major role in determining which coupling is more suitable. In general, Servoflex couplings are ideal for small and lightweight applications, such as servo or stepper motors. Typical product advantages such as low mass inertia, fast reaction and very high torsional stiffness are typical of servo discs. Servoflex couplings are ideal for low or very low torque and shaft size requirements with low load requirements. Composite Disc couplings are ideal for applications with high requirements in terms of torque capacity and misalignment compensation in combination with large bore diameters. Application-specific factors are decisive in selecting the optimum coupling. These factors often include:
- Torsional stiffness
- misalignment or misalignment error
- Torque requirement
- Vibrations
- Shock load
- Operating mode
- Environmental requirements (temperature, media)
- and much more
We recommend contacting Zero-Max directly for the optimum choice of coupling.
What is Axial Natural (ANF) and what advantage does it offer?
The heart of every composite disc coupling is the revolutionary disc pack made of high-performance composite disk material. As a basic property, the fiber composite material of the disc pack has an axial stiffness with a linear characteristic profile. The calculable axial natural frequency (ANF) can be determined based on this basic property of the disk material. This offers the advantage of allowing the natural frequency range to be calculated, thus offering smooth operation and preventing vibrations.
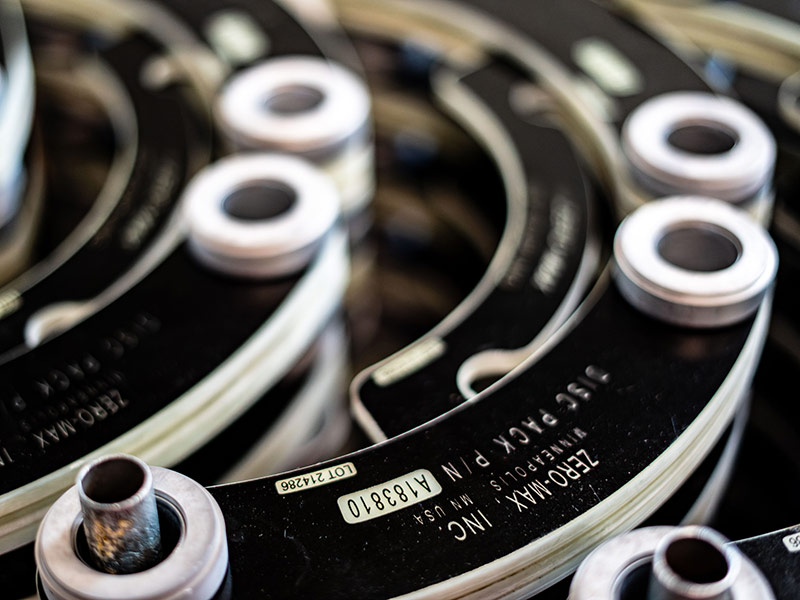
What special designs are available for bores or keyways?
Bore diameters are available in metric and imperial dimensions, customized or individual bore designs are possible.
- Conical bores
- Thread versions
- Spline profiles (e.g. SAE)
- Special keyways
- Customer-specific tolerances
- Specific dimensional requirements
- and much more
Zero-Max offers the AGMA and ISO standards as standard versions for keyways, other versions are available on request.
Does Zero-Max produce larger couplings than specified in the catalog?
Zero-Max developed and produced couplings for the renewable energy sector back in the early 1990s. This special area of application presents particular challenges that need to be overcome. In the past, for example, wind turbine systems from reputable manufacturers could be equipped. As a result of these past challenges, Zero-Max has the know-how and the necessary expertise to offer coupling solutions that go beyond the usual standard. For application requirements outside of the catalog values, please contact us directly.
What can Zero-Max offer in the case of high-speed requirements?
All Zero-Max coupling designs are specified with a maximum operating speed as standard (catalog). The specification of the maximum permissible speed takes into consideration the coupling size, model series and the corresponding hub design. For application specifications that exceed the specified speed value, please contact us directly for a customized solution. If necessary, an appropriate result can be achieved by dynamic balancing, the reduction of misalignments and/or a service life analysis.
How large should the minimum shaft engagement of a CD coupling with clamping hub connection?
Ideally, the entire hub length should enclose the shaft (catalog dimension “B”). The shaft can also extend beyond the hub ends into the area of the disk pack, but should not contact the disk pack (dimension “H” in the catalog) or the shaft on the opposite side. If it is not possible to cover the entire hub length, it must be ensured that the bending capacity of the clamping hub is available for torque transmission. As a rule, the required bending area corresponds to approx. 2/3 to 3/4 of the total length of the clamping hub, depending on the size of the coupling. Please contact us if you have any further questions.
Why a composite disc coupling can be a real alternative to a classic metal bellows coupling?
The requirements demanded of a specific system are often individual and no general statements can be made about the preferred products. If the basic properties of the composite disc coupling and metal bellows couplings are compared, specific properties can be determined. Metal bellows couplings often have a very high torsional stiffness and generally more brittle than CD couplings. For application requirements with frequent and rapid load changes, or reversing and indexing processes, composite disc couplings often offer better properties in terms of reaction loads compared to metal bellows couplings. Metal bellows couplings tend to transfer forces to connected components under frequent load changes, which can lead to damage or failure.
Advantages of the composite disc:
- Better shock load capacity
- Ideally suitable for indexing and reversing operation
- Ability to absorb fatigue-free alternating loads
- Coupling does not have to be completely replaced for maintenance or replacement (disk pack replacement)
- Higher misalignment compensation (compensation of misalignment or alignment errors)
- Lower mass inertia
- Lower reaction loads prove to be ideal for torque transducers
- Prevents grooving in bearings – electrical insulation
(example encoder or rotary encoder applications) - High chemical resistance
- High level of customizability to application requirements possible
(bellows coupling manufacturers are often tied to metal bellows manufacturers) - and much more
Why are the nominal and peak torques explicitly stated in the data sheets?
Nominal torque is the torque that can be applied 365 days a year under normal operating conditions (24/7). The peak torque is the torque load (start-up process, emergency stop situation) with short-term torque peaks that affect the system. If the nominal or continuous torque is frequently exceeded, the service life of the coupling is reduced.
What if the standard Zero-Max products are not suitable?
For applications or requirements that require a customized or individual design, Zero-Max offers the option of an FEA analysis (Finite Element Analysis). Application-specific modifications or changes to the disk design or changes to the composite material can be designed or analyzed according to the requirements. State-of-the-art systems and programs enable Zero-Max to provide reliable and unique solutions that differ from products from the standard portfolio.
Do you have questions about the product? Click here for expert advice.